Dr. Manuela Kummeter
Business Consultant for Operational Excellence
Expert Positive Leadership
Coach for Leaders in Industry
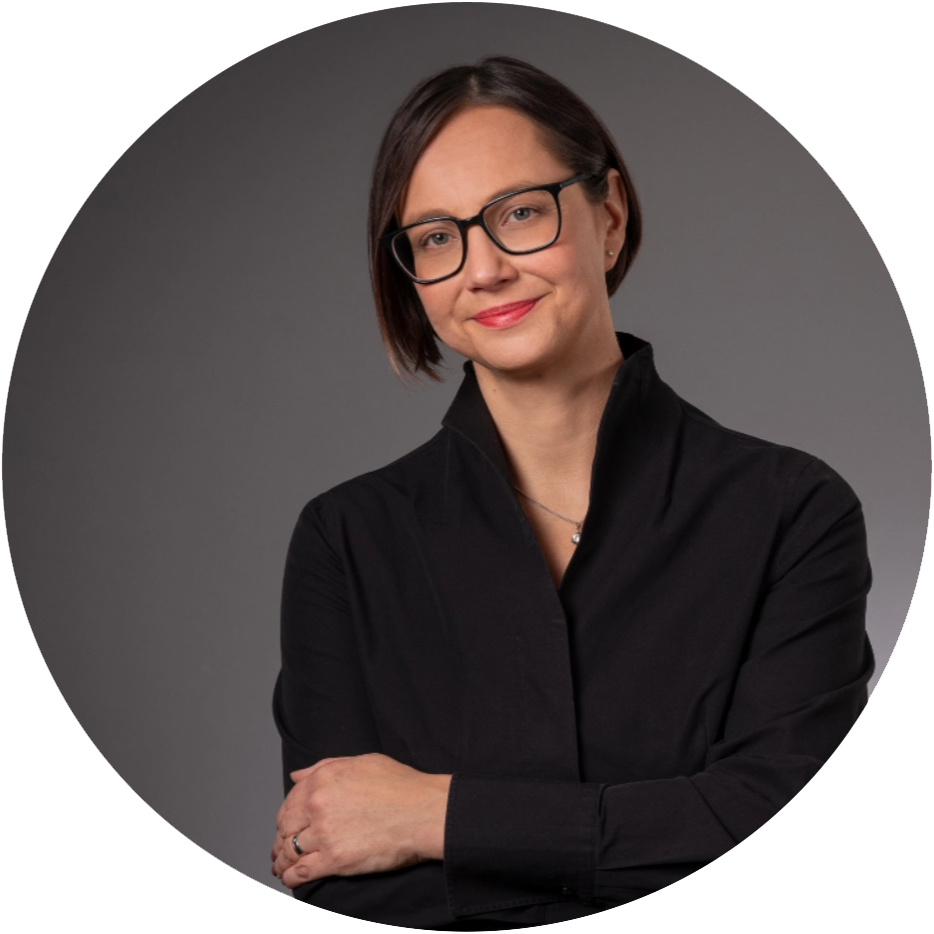
Connection and flow for tough targets
I strengthen (wo)man and machines: because excellence in value chains comes from trust, enthusiasm and stable yet flexible processes. We’ve had enough crisis!
My customers
I support industrial customers throughout Europe. My focus is on the process industry, as this is where my roots are: I have worked myself for 15 years in various positions as an employee and leader in technology, operational excellence, regional, site and global units at BASF and AkzoNobel.
From small to medium-sized companies to large corporations: I develop a suitable program for everyone based on the corporate culture. Every production site has its own peculiarities and problems. That’s why standard solutions don’t help. Together we discuss where the problem lies and which issues need to be addressed. Is it the path to the end-to-end supply chain? The management culture? Or an investment or maintenance plan that finally needs to be implemented? We use methods from the fields of LEAN management, positive leadership and diversity management and my specific method of PoLean.
European, pragmatic and humorous
The European process industry has been in an almost uninterrupted crisis for 15 years. A good opportunity to try something new! Because for me as a Cologne native: Et kütt wie et kütt un et hätt noch jot jejange – whatever happens does happen and in the end it will be good! Being creative and innovative has never been as important as it is now. But fear kills creativity!
That’s why I support employees and managers to work in a self-determined way. Together we breathe life into the buzzword ‘empowerment’ in the process industry. To do this, I combine lean management methods with scientific findings from positive psychology. Instead of tools, I offer pragmatic implementation.
“One of the very important concepts of TPS
is total participation.” - Ritsuo Shingo
An organisation is only as good as its employees. And employees are only as good as the organisation allows them to be. When Toyota introduced the Toyota Production System (TPS) in the 1980s, the inventors based it on precisely this principle.
In Europe and especially in Germany, however, for a long time the focus was only on the tools: 5s, TPM, SMED,…
In my service offering, I combine methods from LEAN management with the missing element of culture. However, as this cannot simply be copied and pasted from the TPS, I build it on elements of the European OpEx culture. And I combine it with insights from positive psychology.
PoLean is OpEx 2.0
- It supports dialogue between departments and hierarchical levels.
- Optimises the entire value chain.
- Enables quick reactions in times of crisis and flexibility when plans are changed.
- Strengthens the psychological capital of employees.
OpEx culture is doing things with enthusiasm
Together we implement. Because for me, a consultation never ends with just a concept. In the spirit of continuous improvement, we ideally turn the wheel together once. Because then we know what works and what doesn’t. And adapt.
Training and skills
- Lean management and KATA coaching
- Lean Six Sigma Yellow Belt
- PR consultant/PR consultant PZOK (DPRG)
- Certified Perma Lead Consultant
- Diploma of Advanced Studies Positive Psychology and Coaching, DHGS
- Positive Psychology and Coaching (M.A. in training), DHGS
- PhD, Organic Chemistry, University of Heidelberg
- Diploma in Chemistry, University of Saarland
More about me: Link to LinkedIn-Profile